necessary that the sand lies smooth and even at all times. When the workman has rolled up ten or fifteen yards, he cuts it across with a knife and straightedge, so that the paper is cut at right angles with its sides.
There are three different sorts of roofing paper, according to the impregnating fluid used in its manufacture. The ordinary tar paper is that saturated with clear cold tar. This contains the greatest amount of fluid ingredients and is very raggy in a fresh condition. It is easy to see that the volatile hydrocarbons evaporate in a short time, and when expelled, the paper becomes stiffer and apparently drier. This drying, or the volatilization of the hydrocarbons, causes pores between the fibers of the paper. These pores are highly injurious to it, as they facilitate a process of decomposition which will ruin it in a short time.
Roofing paper can be called good only when it is essentially made from woolen rags, and contains either very few or no earthy additions. It is beyond doubt that the durability of a roofing paper increases with the quality of wool fiber it contains--vegetable fibers and earthy additions cause a direct injury. Reprehensible altogether is any combination with lime, either in form of a carbonate or sulphate, because the lime enters into chemical combination with the decomposition products of the tar.
The general nature of gravel is too well known to require description. The grains of quartz sand are either sharp cornered or else rounded pieces of stone of quartz, occasionally mixed with grains of other amorphous pieces of silica--such as horn stone, silicious slate, carnelian, etc.; again, with lustrous pieces of mica, or red and white pieces of feldspar. The gravel used for a tar paper roof must be of a special nature and be prepared for the purpose. The size of its grains must not exceed a certain standard--say, the size of a pea. When found in the gravel bank, it is frequently mixed with clay, etc., and it cannot be used in this condition for a roof, but must be washed. The utensils necessary for this purpose are of so simple and suggestive a nature that they need not be described. Slag is being successfully used in place of the gravel. It is easily reduced to suitable size, by letting the red hot mass, as it runs from the furnace, run into a vessel with water. The sudden chilling of the slag causes it to burst into fragments of a sharp cornered structure. It is next passed through a sieve, and the suitably sized gravel makes an excellent material, as it gives a clean appearance to the roof.
The thinking mind can easily go one step further and imagine that, since the tar contains a number of volatile hydrocarbons, it might be made more adaptable for impregnation by paper by distilling it, as by this process the fluid would lose its tendency to evaporate and the percentage of resinous substances increase. Singular to say, there was a prejudice against the employment of distilled tar, entertained by builders and people who had no knowledge of chemistry. Increasing intelligence and altered business circumstances, however, brought about the almost universal employment of distilled tar, and every large factory uses it at present. The roofing paper prepared with distilled tar is perhaps most suitably called asphaltum paper, as this has been used in its manufacture. It possesses properties superior to the ordinary tar paper, one of which is that immediately after its manufacture, as soon as cold, it is dry and ready for shipment; nor does it require to be kept in store for a length of time, and it has also a good, firm body, being as flexible and tough as leather. It is very durable upon the roof, and remains flexible for a long time. It is true that asphaltum papers will always in a fresh state contain a small percentage of volatile ingredients, which after a while make it hard and friable upon the roof; but, by reason of its greater percentage of resinous components, it will always preserve a superior degree of durability and become far less porous. One hundred parts by weight absorb 140 or 150 parts by weight of coal tar. A factory which distilled a good standard tar for roofing paper recovered, besides benzole and naphtha, also about ten per cent. of creosote oil, used for one hundred parts raw paper, 176.4 partially distilled tar. Experiments on a larger as well as a smaller scale reduced this quantity to an average of 141.5 parts for one hundred parts raw paper. The weight of sanded paper is very variable, as it depends altogether upon the size of the sand grains. It may be stated generally that the weight of the sand
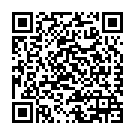
Continue reading on your phone by scaning this QR Code
Tip: The current page has been bookmarked automatically. If you wish to continue reading later, just open the
Dertz Homepage, and click on the 'continue reading' link at the bottom of the page.