although the Navajos have often seen
these wheels, have had abundant opportunities for buying and stealing
them, and possess, I think, sufficient ingenuity to make them, they have
never abandoned the rude implement of their ancestors. Plate XXXIV
illustrates the Navajo method of handling the spindle, a method
different from that of the people of Zuñi.
They still employ to a great extent their native dyes: of yellow, reddish,
and black. There is good evidence that they formerly had a blue dye;
but indigo, originally introduced, I think, by the Mexicans, has
superseded this. If they, in former days, had a native blue and a native
yellow, they must also, of course, have had a green, and they now make
green of their native yellow and indigo, the latter being the only
imported dye-stuff I have ever seen in use among them. Besides the
hues above indicated, this people have had, ever since the introduction
of sheep, wool of three different natural colors--white, rusty black, and
gray--so they had always a fair range of tints with which to execute
their artistic designs. The brilliant red figures in their finer blankets
were, a few years ago, made entirely of bayeta, and this material is still
largely used. Bayeta is a bright scarlet cloth with a long nap, much
finer in appearance than the scarlet strouding which forms such an
important article in the Indian trade of the North. It was originally
brought to the Navajo country from Mexico, but is now supplied to the
trade from our eastern cities. The Indians ravel it and use the weft.
While many handsome blankets are still made only of the colors and
material above described, American yarn has lately become very
popular among the Navajos, and many fine blankets are now made
wholly, or in part, of Germantown wool.
The black dye mentioned above is made of the twigs and leaves of the
aromatic sumac (Rhus aromatica), a native yellow ocher, and the gum
of the piñon (Pinus edulis). The process of preparing it is as follows:
They put into a pot of water some of the leaves of the sumac, and as
many of the branchlets as can be crowded in without much breaking or
crushing, and the water is allowed to boil for five or six hours until a
strong decoction is made. While the water is boiling they attend to
other parts of the process. The ocher is reduced to a fine powder
between two stones and then slowly roasted over the fire in an earthen
or metal vessel until it assumes a light-brown color; it is then taken
from the fire and combined with about an equal quantity in size of
piñon gum; again the mixture is put on the fire and constantly stirred.
At first the gum melts and the whole mass assumes a mushy
consistency; but as the roasting progresses it gradually becomes drier
and darker until it is at last reduced to a fine black powder. This is
removed from the fire, and when it has cooled somewhat it is thrown
into the decoction of sumac, with which it instantly forms a rich,
blue-black fluid. This dye is essentially an ink, the tannic acid of the
sumac combining with the sesquioxide of iron in the roasted ocher, the
whole enriched by the carbon of the calcined gum.
[Illustration: PL. XXXIV.--NAVAJO WOMAN SPINNING.]
There are, the Indians tell me, three different processes for dyeing
yellow; two of these I have witnessed. The first process is thus
conducted: The flowering tops of Bigelovia graveolens are boiled for
about six hours until a decoction of deep yellow color is produced.
When the dyer thinks the decoction strong enough, she heats over the
fire in a pan or earthen vessel some native almogen (an impure native
alum), until it is reduced to a somewhat pasty consistency; this she adds
gradually to the decoction and then puts the wool in the dye to boil.
From time to time a portion of the wool is taken out and inspected until
(in about half an hour from the time it is first immersed) it is seen to
have assumed the proper color. The work is then done. The tint
produced is nearly that of lemon yellow. In the second process they use
the large, fleshy root of a plant which, as I have never yet seen it in
fruit or flower, I am unable to determine. The fresh root is crushed to a
soft paste on the metate, and, for a mordant, the almogen is added while
the grinding is going on. The cold paste is then rubbed between the
hands into the wool. If the wool does not seem to take the color readily
a little water is dashed on the mixture of wool and
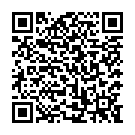
Continue reading on your phone by scaning this QR Code
Tip: The current page has been bookmarked automatically. If you wish to continue reading later, just open the
Dertz Homepage, and click on the 'continue reading' link at the bottom of the page.